在现代电子产品的制造中,印刷电路板组装(PCBA)是整个生产链中的关键步骤。PCBA的质量直接关系到设备的性能和可靠性。因此,从贴片到老化测试,每一个环节都不容忽视。了解驱动PCBA加工全流程,有助于提升生产效率和产品质量。以下将详细介绍驱动PCBA加工过程中的15个重要环节。
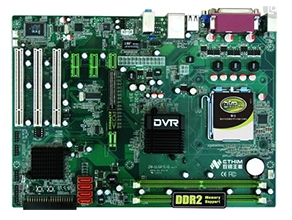
一、元件准备
在任何PCBA加工流程的开始,合理准备元件至关重要。生产团队需确保所有元件已按照设计图纸进行检验和分类,确保元件的数量与规格符合生产要求。
二、PCB表面清洗
在贴片前,必须对PCB板进行表面清洗,去除尘埃、油脂和氧化物,以确保焊接的可靠性。清洁的表面提升了焊接的附着力,降低了后续故障的风险。
三、印刷焊膏
焊膏的印刷是SMT(表面贴装技术)流程中的重要一环。通过高精度的印刷技术,将焊膏准确地印刷到焊盘上,确保后续元件的焊接质量。
四、元件贴片
元件贴片环节中,快速、高效的贴片机会根据设计文件把各类元件准确地放置到PCB上,确保其位置精确无误。这一环节直接影响到后续的焊接效果。
五、回流焊接
通过回流焊接过程,将已贴好的元件与焊膏结合,实现元件的紧密焊接。焊接过程中的温度曲线需要精准把控,以确保焊接质量达到标准。
六、视觉检查
焊接完成后,进行视觉检查非常关键。通过高倍镜或自动视觉检测系统,观察焊点质量、元件位置等,确保无焊接缺陷。
七、功能测试
此环节对每个组装好的电路板进行功能测试,以确保其正常运行。通过测试仪器检测各个电路块,确保每个功能模块都按设计要求工作。
八、老化测试
通过老化测试,验证电路板的稳定性和耐用性。该测试通常在特定的温度和湿度条件下进行,以模拟长期使用中的各种环境因素。
九、环境适应性测试
在不同的湿度和温度条件下,评估PCBA的性能。通过模拟实际使用环境,确保产品在极端条件下仍能正常工作,符合产品的可靠性要求。
十、极限测试
对PCBA进行极限负载测试,以验证其在极限条件下仍能保持功能。这一步骤帮助识别潜在的故障点,并确保产品的安全性。
十一、清洗流程
PCB组装完成后,必要的清洗步骤去除焊接过程中残留的焊膏、腐蚀物质及其他污染物,确保产品符合清洁标准。
十二、标识与包装
经过各项测试合格后,PCBA将进行标识和包装。清晰的标识确保在后续生产或使用中能够明确识别该电路板的型号与特性。
十三、仓储管理
为确保产品的质量,合理的仓储管理显得尤为重要。在适宜的环境条件下存放,防止潮湿、温度变化对产品的影响,确保产品在发货时处于正常状态。
十四、出货前检查
在产品发货前,进行最后的质量检查,包括数量、规格和包装等,确保每一项符合客户的要求。
十五、客户反馈与改进
在产品交付给客户之后,及时收集客户反馈,评估产品在实际使用中的表现。这一环节是持续改进的重要依据,为生产过程的优化提供数据支持。
驱动PCBA加工全流程从元件准备到客户反馈,每一个环节都有其重要性。通过对15个加工环节的系统了解,企业能够有效规避在生产过程中的潜在风险,提升产品的质量。这一系列严谨的流程,不仅确保了产品的功能与性能,更是企业信誉和市场竞争力的重要保障。